In this first post, I will tell you a little about how it started. Well, for more than 10 years ago, just at the beginning of my membership in “Swedish Electronics Forum”, I read about some members who built computer-controlled milling machines. It was, for example, a machine that went by the name Little sister.
A little interest in building my own machine began to grow in the back of my mind. However, there was so much else that occupied my time so nothing happened until now, many years later. I had in fact collected some mechanical scrap that could be used for a “scrap construction” of the simplest kind without me having to buy a lot of material.
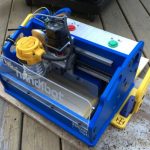
I started looking at what was on Yoytube and found a design that I thought was a good project to build. It was called Handibot, it was a small machine that could mill on unlimited large subjects. You just moved it over the surface to be milled, yes you could even hang it on the barn door and mill in a picture of your favorite cow.
When I started drawing the machine in my CAD program, I realized that it would be good to have a cutter that could mill out the parts to it to get a perfect fit on mounting holes etc. I then started building a temporary milling table of plywood and scrap details. As a milling motor, I used an old handheld wood router that I bought at Biltema many years ago and discarded due to a new purchase. Since I would only use it to make components consisting of 12 mm Corian, the milling height was made to only 20 mm for the sake of simplicity. It would only handle the 12 mm. Corian plates. Here is a link to a video that shows how I thought. Unfortunately I speak Swedish but the video shows how it is intended to be.
From the beginning, I only intended to maneuver the movements over the Corina plate both in length, width and height by hand and use digital calipers to keep track of where I would drill / mill. During the construction, however, I realized that I could easily use some old stepper motors that I had removed from old system printers that I had scrapped earlier. I had bought drive electronics for these from Ebay as spare parts for another project, but we can take that another time.
Here is a link that shows the first test with motors for deep movement (Y-axis). So now it was basically a CNC milling machine in progress, a real “scrap building” but still. It would be able to help me get parts for a better cutter, that was at least my plan. Eventually, it was time for a test run of the provisionally folded CNC milling cutter. Here is a link to the video where I mill out the first test piece Do not miss the continuation of what is happening in the Carvers Corner.
Finally, please be tolerant of my English. I belong to the old generatione (75 years old), who did not study much English in school. Have a nice day.
Leave a Reply